The TAPAS (Made in India Drone) had to go! Thankfully, it has gone! The mission mode project will reportedly not be funded by the Indian MoD anymore. The decision to defund the project was objective and based on logic for the following reasons:
-
Performance shortfalls were substantial. The gaps were too wide and beyond redemption.
-
The airframe configuration chosen for the drone severely limited DRDO’s ability to address the performance shortfalls.
-
The lack of a suitable turboprop powerplant put the DRDO at a dead end.
Flawed Design
Most successful military UAVs use a single-engine, twin-boom design (SETB) with a turboprop engine featuring a pusher propeller fitted aft of the fuselage.
Examples of SETB design UAVs include the Israeli Searcher and Heron drones, both of which are in service in the Indian armed forces, Turkey’s Bayraktar TB2 and India’s Rustom-1, now renamed Archer,
A twin-boom design increases overall aerodynamic efficiency and reduces drag. The wider fuselage facilitates fitting sensors and generates body lift, allowing for a shorter wingspan.
The design provides a clean and stable platform with a longer range, higher fuel efficiency, and better maneuverability. The UAV is structurally stronger. In case of an engine failure, the SETB design facilitates a longer-range glide.
The SETB design keeps the power plant as far away from the payload and sensors to minimise thermal and vibration interference.
The other advantages of the SETB design include
-
It facilitates modular construction, simplifying assembly, maintenance, and potential upgrades.
-
Easy engine accessibility makes maintenance and repairs quicker and more cost-effective
-
Avoids weight and fuel efficiency penalties accruing from the use of two engines
-
Fewer components compared to twin-engine designs translate to lower weight, simpler systems, and potentially higher reliability
Other Conventional Design Twin Engine UAVs
Wing mounted engines, that too diesel engines, make little sense. Diesel engines are known to cause more noise and vibration.
UAVs that don’t use a twin boom fuselage layout, such as the US Predator and the Russian Orion, still opt for aft-mounted turboprop engines with pusher propellers. They are quieter and more efficient.
Diesel Engine Powered / Conventional Fuselage UAVs Do Exist
UAVs powered by two wing-mounted diesel engines do exist. But a twin-engine configuration is more suited to a heavy UAV.
The Russian Altius is an example of a UAV powered by two wing-mounted diesel engines, like the TAPAS. However, the Altius is a 6t-7t combat drone with a 28.5m wingspan, designed to carry a 2t payload. In contrast, TAPAS was conceived as a 2t UAV.
The conventional fuselage configuration is better suited to heavier drones or unmanned transport aircraft. It’s reported that the Altius will also be ultimately powered by a turboprop derivative of the Russian VK-800S fifth-generation turboshaft engine.
Interestingly, the Altius has been long under development and is yet not known to be operational. A recent report indicated that its projected payload has been reduced to 1 t, suggesting weight spiral issues similar to the TAPAS.
Turkey’s Bayraktar Akıncı is a rare example of a successful conventional fuselage twin-engine UAV. Once again, it is a bigger aircraft with a maximum take-off weight (MTOW) of 5.5+ tons and a payload of over 1,350 kg. However, the Akıncı is powered by two turboprop engines, of either 450 hp or 750 hp.
TAPAS Weight Spiral
During development, the Tapas project was severely impacted by a weight spiral that resulted in the AUW (All Up Weight) of the aircraft going up from the planned 1800 kg to 2800 kg.
One of the reasons for the weight spiral was reportedly the switch from composite to metal tank as a result of frequent fuel leaks.
The weight spiral mandated the following measures to cope with it.
-
Use of higher power engine
-
Re-design of Engine Interface Module & Nacelle
-
Local reinforcement/stiffening of the span of the wing
-
Re-sized VT (Vertical tail to make the rudder more effective)
-
Aerodynamic re-design (Twin Element Airfoil) for meeting QR
-
Increased takeoff & landing distance
-
Increase in minimum loiter velocity
-
Reduced endurance
-
Reduced ceiling
-
Wing twist to mitigate the tip stall at a higher roll rate during approach for landing
ADE’s desperate measures to mitigate the weight spiral included
-
Integrating avionics package in a single LRU (70-80 kg weight reduction)
-
Airframe weight optimization (180-kg reduction) by using lighter material.
-
Reducing the safety factor from 1.5 (the standard for manned aircraft) to 1.25 in a gradual manner.
At best, DRDO aimed to reduce the weight by 280 kg!
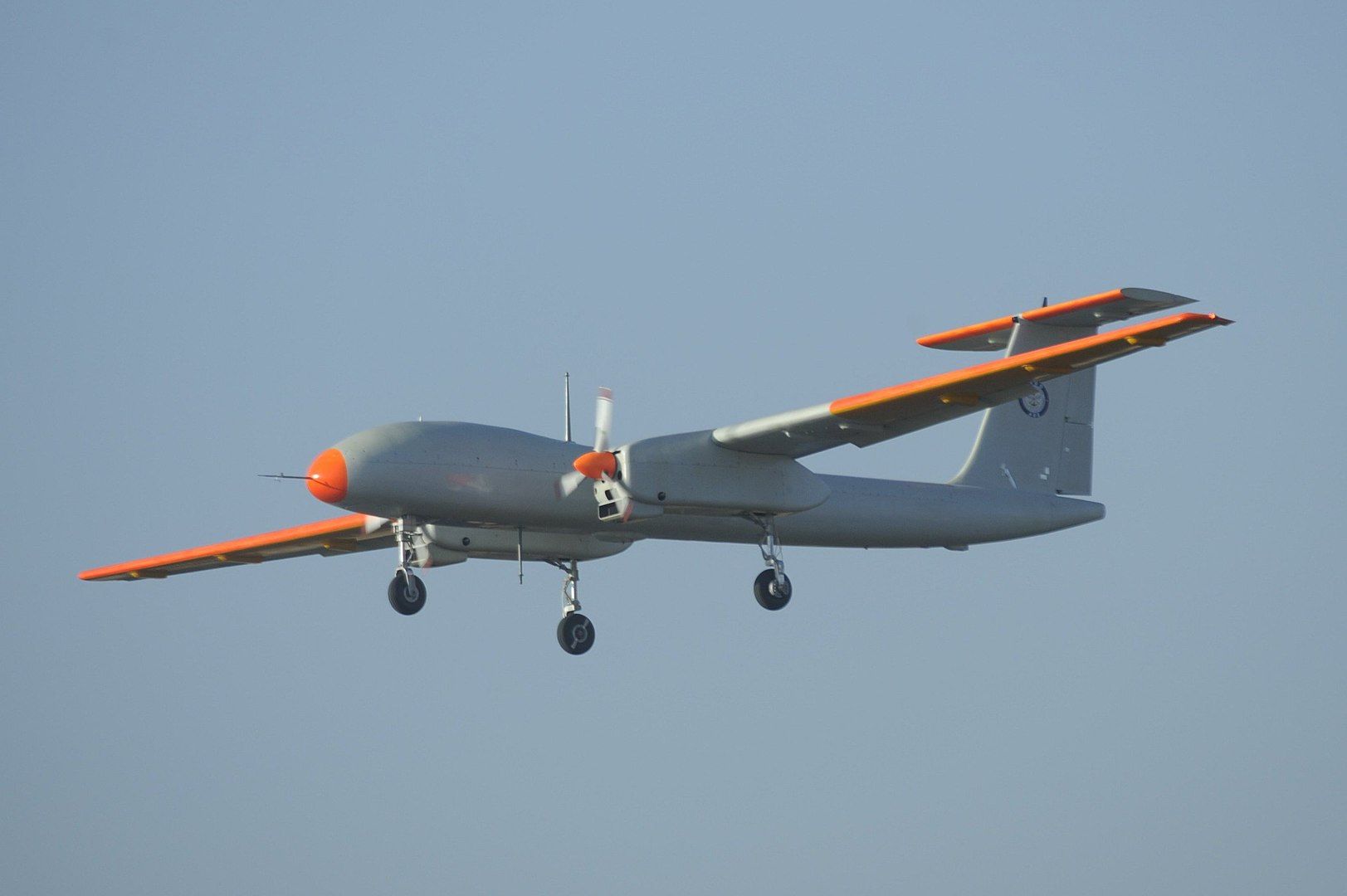
Questionable Decisions
At Aero India 2017,. DRDO displayed a diesel engine-powered Tapas. But at Aero India 2019, DRDO, for the first time, displayed the Tapas MALE drone powered by NPO-Saturn 36MT turboprop engines delivering a thrust of around 73.55 kW (~100 hp) each.
However, it also displayed a scale model of the Tapas with a diesel engine. A DRDO official contended that the final power plant is yet to be finalized!
Clearly, DRDO’s decision-making was guided by something beyond objective thinking. Hopefully, it wasn’t pressure to use an indigenous diesel engine in a destructive and misplaced quest for Atama Nirbharta (self-reliance)!
Conclusion
The limitations of the TAPAS design have been evident to ADE for over a decade. ADE has also been aware that it would not be able to adequately address the weight spiral. And consequently, the drone’s performance would fall well short of the QRs.
Under the circumstances, the decision by the DRDO management to still pursue the project was a disservice to the nation. It likely held back the launch of an alternative project and also led the Armed Forces up the garden path. Not fair!
- Vijainder K Thakur is a retired IAF Jaguar pilot. He is also an author, software architect, entrepreneur, and military analyst. VIEWS PERSONAL OF THE AUTHOR
- Follow the author @vkthakur